English Section
Publicat de Ovidiu Stefanescu
29 Aug 2016 09:49
|
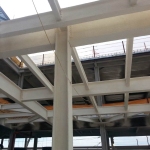 Modern science provides numerous special passive fire protection solutions, many of which are designed to protect steel structures from the destructive effects that high temperatures can exert on them. The methods proposed by experts in order to achieve that objective fall into two main categories - namely non-reactive (panels and sprays) and reactive, of which the most representative consist of intumescent coatings fall in the category of "thin -film (which can be applied directly on site or in the workshop). Of course, there are situations that require a combined use of this solutions, and this is why ins necessary a correct understanding of phenomena. The intumescent coating systems consist generally into three distinct components: primer, base or principal coat (which react directly with fire) and sealing coating. As it is easy to guess, the most important element is the second one and that includes a catalyst that decomposes to produce the necessary mineral acid for the process (e.g., phosphoric acid), a charred coal, such as starch, which reacts with the acid and generates the charcoal, a binder or a resin which has the function to soften the composition at a preset temperature and a foaming agent that decomposes along with the binder, generating large volumes of non-combustible gas (carbon dioxide, ammonia and water vapor, facilitating charcoal swelling and forming thus the insulating layer, which has a thickness of several times greater from baseline measured before exposure to the flame heat). Basically, these outstanding technical solutions are inert to normal temperatures but provides an excellent insulation to 200 ° C - 250 ° C, making the protected material (steel) not to be affected. Solutions ranging from "thin-film" is used in those projects where the requirements for fire resistance are 30, 60 or 90 minutes, but in recent years have been developed combinations which provides protection for a period of 120 minutes.
|