English Section
Publicat de Ovidiu Stefanescu
28 Iun 2016 10:26
|
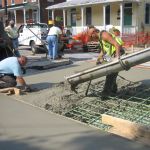 The history of concrete additives is long and begins in 1930, when were registered the first attempts to disperse coal in a concrete mixture. The original purpose was purely aesthetic, and main applications aimed at differentiation of the highway bands, signalling the danger zones. The results of this procedure were not as expected, added particles rising to the surface and giving it a mottled appearance. Another disadvantage was related to impairment of mechanical resistance characteristics. To fix the problem, the chemistry specialists have proposed using a vintage dispersing agent which, as demonstrated subsequently, exerted a beneficial effect on the entire material, including the ensuring of an optimal mixing of the cement components. Furthermore, by including a substance called triethanolamine, it was obtained the effect of delaying the process, which revolutionized the procedures of concrete production. Currently, there is developing a veritable industry dealing with additives for concrete, which facilitates the use of these materials in the most unexpected works and ensure optimum performance and durability. The main ingredients of the Portland type of cement are lime, silica, alumina and iron oxide. The first component is obtained by extraction from deposits of limestone and alkaline industrial waste. Regarding the other three elements, they are derived from clay, shale and slag or ash residues resulted from coal-fuelled power plants. The materials are mixed and transformed into a very fine powder, which is processed in a rotary kiln, at a temperature of 1500 ° C. In this environment the chemical reactions are finalized, getting the four basic components of cement – namely: dicalcium and tricalcium silicate, tricalcium aluminate or tetracalcium aluminoferrite. All of those substances, along with a minor amount of calcium hydroxide and other oxides, form the so-called clinker leaving the furnace, subsequently receiving a hydrated calcium sulfate add (gypsum). This leads to the end product - Portland cement, also known as "hydraulic" cement, characterized by enhanced compressive strength when it is hydrated.
|